You are probably talking about storage units, but we know what you mean. It’s a…
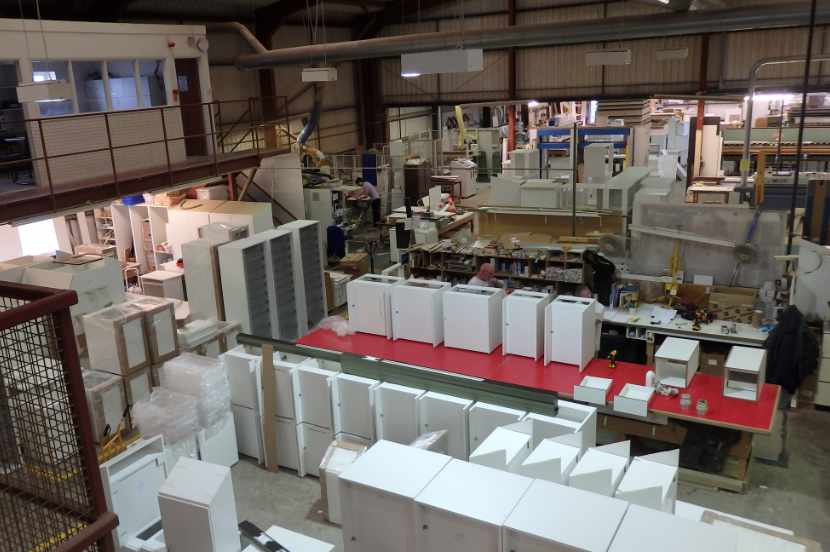
Here’s how a furniture supplier’s manufacturing process should look: from start to finish
Manufacturing furniture may sound like a pretty standard process amongst all manufacturers, but this process can be a nightmare when communication is poor, and processes are thus not correctly understood. Peeking inside the manufacturing process from start to finish and understanding what expectations you should have as a client (contractor, architect, project manager or procurement) can help you spot the best manufacturers before entering the process.
Enquiry
From the moment an enquiry is submitted with a prospective furniture supplier, it’s reasonable to have immediate expectations of them. How they engage from the first moment is an indicator of how they engage and communicate moving forward. In this initial interaction, contractors, architects and project managers will want to scrutinise the communication between them and the supplier.
At DBFS, our enquiries typically come in a few forms. Some will send us a list of furniture requirements. Others will send drawings of the rooms and details on how they would like them fitted out. If the information submitted is not enough to confidently structure a quote, we will come back with questions to ensure we have the information right. Once we’ve confirmed we have all the information needed to quote the work, we will structure a detailed quote, with specifics included:
- Product codes
- Colours
- Descriptions
- Per piece prices
- Delivery dates
- Installation dates.
Ordering
When an order is placed, the real relationship begins. Suppliers should communicate the steps they’re taking, sharing details of their approach so that clients are confident the job is being done on time and to scope.
When an order is received at DBFS, we check the information on the order against the original quote and add any up-to-date drawings. If it’s needed as part of the order, we can do these technical drawings for the project in-house. This service is often required for normal storage furniture or special items like reception counters.
With all the order information gathered, we would send an order confirmation, acknowledging and reconfirming all of the details included in the order, as well as our own next steps. The paperwork for the order goes to our production manager, who assesses the job, checks stocks of materials and makes any orders necessary for the job’s materials — such as laminate, board, mirrors, hooks, hinges, locks. Everything needed to start manufacturing.
Production
As will have been agreed when the order is placed, the production begins a few weeks before the delivery date. This is plenty of time for our team to produce the furniture, and waiting until this point also allows clients to request changes, should they be necessary, without any waste (of both materials and budget).
Once production begins, the process of producing furniture for the order goes as follows:
Beginning at the beam saw, we cut the large sheets of board material to the required panel sizes. We then move to the edge bander, which applies edging to all the panels. Next comes the C&C drill. This drills the various holes in the panels, ready to receive the dowels, which are put in place and glued to fix the various panels together to form the unit shape.
Moving on over to the carcass press, we build the carcass for each unit. And while this is going on, the doors for the unit (if it’s a storage unit) are being made.
Once these steps have been taken, the two jobs come together, and the doors and feet are put on. The drawers are put in — if required — and the cabinet is then finished.
In the case of worktops, the worktop and joinery departments may also be involved, bringing together three jobs, such is the case if a reception counter is being made, for example.
All complete, the furniture is cleaned, wrapped and sent to the warehouse, where it is marked and ready for delivery.
Healthcare furniture manufacturing process – find out more
The team at David Bailey Furniture Systems pride ourselves on our communication and our flexibility. Being UK based, we have agility that is unique and extremely valuable to our clients. For a smooth production process, with strong communication throughout, contact our team today. You can also read some case studies here about healthcare and hospital installations where we have installed our furniture.