You are probably talking about storage units, but we know what you mean. It’s a…
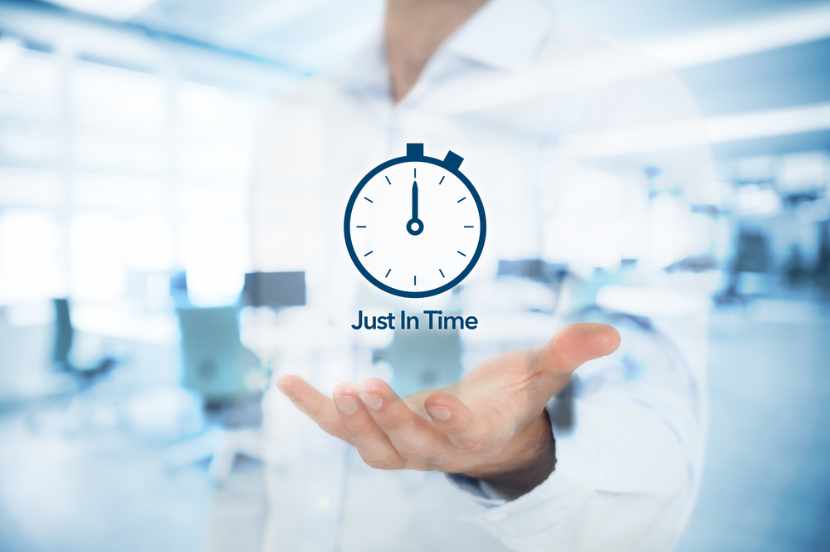
What is Just in Time manufacturing and why do you want it from your furniture supplier?
If you’re engaging with, or researching, a furniture manufacturer, you’ve probably come across the term: just-in-time manufacturing. It’s commonly promoted somewhere on a website. And many companies, including ours, work this way.
So, what is it? We talk about just in time (JIT) manufacturing a great deal with our clients, but we realise that not everyone comes to us with knowledge of this manufacturing methodology. Thus, they don’t understand how it impacts the results for them.
What is just-in-time manufacturing?
Just-in-time manufacturing, or (Just in Time concepts) focuses on producing exactly the amount that is needed at exactly the time a customer needs it. On the other hand, traditional manufacturing means making things ahead of time and selling them to customers.
Within the Agile manufacturing methodology, JIT manufacturing is one of the stages. The Agile philosophy is about adding value to the customer by focusing on rapid response. This style allows manufacturers to take advantage of short windows of opportunity and fast changes in customer demand.
How JIT manufacturing impacts furniture making
We will speak from our own experience as a JIT manufacturer.
Firstly, the JIT manufacturing approach lets us do more with our space. While we have a warehouse to store furniture before delivery, JIT allows us to move in and out only what is needed. Traditional furniture manufacturing would mean wasted warehouse space and uncertainty about what will sell and what space will be available.
Management of the warehouse also changes with JIT manufacturing. With furniture made as needed, the process is transparent, and staff across departments have greater oversight. Why is that important? There are fewer chances of mistakes and misunderstandings. The stock in the warehouse belongs to a project, and everyone knows what needs to be done for that project and when it needs to be shipped.
No last minute surprises
JIT also helps to minimise wasted time and materials. At DBFS, we monitor our environmental impact and minimise unnecessary waste. Working on the projects we do, where site dimensions and needs can change, JIT ensures that steps and materials aren’t wasted until the project specifications are clear. This benefits everyone.
DBFS manufacture later so that we can site survey the project first. When this is done, we make sure that the furniture specified is going to fit. This means there are no last-minute surprises or problems for our clients, and we can run ahead with projects much faster.
JIT lets us run a smoother operation, with less clutter, less waste, and better efficiency for our clients.
DBFS’ JIT manufacturing process
The manufacturing of furniture is the last step in our work with clients. Before anything is manufactured, there are conversations about the project requirements, and we set up a site survey to minimise surprises. Pipes, for example, often throw up some challenges in furniture manufacturing.
In a typical project, the site survey may be done about two to three weeks before the delivery. This seems late in the project, and that’s exactly the point. Later in the process, other trades will have already been brought in to do their work, which often means some changes. We step in when the layout is officially the final layout after everyone else has been in.
Site surveys allow us to spot any oddities that need to be designed around. When we get to the manufacturing stage, all bases have been covered to make sure the end result gives the expected result.
Flexibility to deal with changes
The JIT process is then managed around the agreed delivery date with our clients. If we know a particular order will take three days to manufacture and get ready, production will start with that schedule in mind, with a bit of contingency planned in.
The agreed delivery date is an important cornerstone of the process, as it ensures that stock does not build up in the warehouse and there is always space to produce new orders. That space also gives us the freedom to switch between jobs and adapt to changes and needs that come up out of the blue. Overall, this flexibility lets us provide a better service for our customers.
Just in Time manufacturing – find out more
All furniture at David Bailey Furniture Systems is manufactured in this way. With JIT manufacturing, we can offer greater customisation while minimising waste and maximising efficiency.
- Visit our online brochure to see our healthcare furniture range
- Read case studies of healthcare furniture projects we’ve carried out
- Or contact us to find out how we may help with your next refurbishment or new build project.