You are probably talking about storage units, but we know what you mean. It’s a…
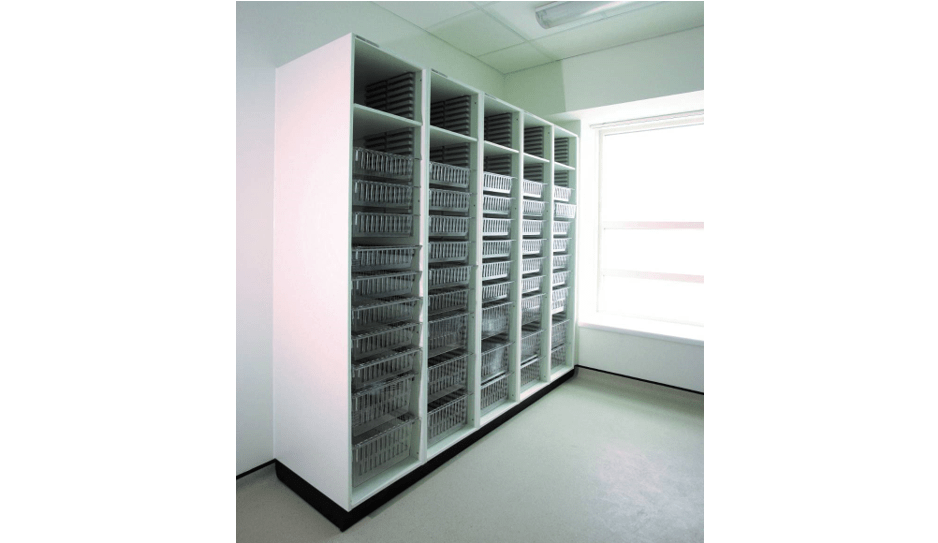
Removing the metals from fitted furniture to make them MRI safe
If you consider that a sophisticated MRI machine, short for magnetic resonance imaging, can cost a UK hospital more than £1.5 million, then you are going to make sure that nothing will ever interfere with its ability to function.
So sensitive are the readings from an MRI scanner that everything around it must be non-magnetic and made from materials that will never interact with the machine’s magnetic field during the imaging process.
It means that the importance of fitted furniture in MRI rooms cannot be overstated, making it a major challenge for companies such as David Bailey Furniture, who have been supplying furniture, fixtures and equipment (FF&E) to UK hospitals for more than 40 years.
The main furniture components, the timber and the melamine facings, are obviously non-ferrous and present no type of threat to a modern MRI scanner, but handles and hinges are – and care has to be taken to ensure that only brass or zinc fittings are used in such environments.
David Bailey Furniture have long been aware of these issues and continue to work closely with NHS Trusts, architects and installers to ensure that its products do not pose any kind of risk within an MRI room.
Research has shown that the use of such non-magnetic products and specialised fitted furniture in MRI rooms can significantly improve patient safety and imaging accuracy. One study, for example, found that the use of non-magnetic products in MRI rooms reduced the number of patient injuries caused by metallic objects entering the machine’s magnetic field.
According to recent statistics, approximately 5 million MRI scans are performed each year in the UK. These scans are used to look for a wide range of medical conditions, such as brain tumours, spinal cord injuries, joint disorders, and heart problems. The high number of MRI scans performed each year highlights the importance of having dedicated MRI rooms in hospitals and medical centres.
Magnetic Resonance Imaging (MRI) was first introduced in the UK in the early 1980s. This ground breaking technology has revolutionized medical imaging and diagnosis, providing high-resolution images of internal body structures that were previously difficult or impossible to obtain.
The development of MRI technology began in the 1940s with the discovery of nuclear magnetic resonance (NMR), a phenomenon in which atomic nuclei in a strong magnetic field absorb and emit electromagnetic radiation. In the 1970s, researchers began applying this principle to medical imaging, using magnetic fields and radio waves to produce detailed images of internal body structures.
The first MRI machines were large, expensive, and complex to operate, limiting their availability to only a few specialized medical centres. Over the years, advances in technology and manufacturing have led to the development of smaller, more affordable MRI machines that can be found in many hospitals and medical centres today.
Operating an MRI machine requires specialised training and expertise. Medical professionals who operate MRI machines, such as radiologists and MRI technologists, must undergo extensive training in MRI physics, anatomy, and patient care. This training typically includes a combination of classroom instruction and hands-on clinical experience.
So, we can see that the technology is awesome but it cannot work in an environment surrounded by ferrous metals. Like all such advances it always gets back to basics and the fitted furniture, shelves and worktops – and the knowledge to ensure they are manufactured to meet the standards demanded for an MRI room – also play a vital role.